Royal Technology provides various R2R metallizers from small to medium, large sizes, more information, please refer to below:
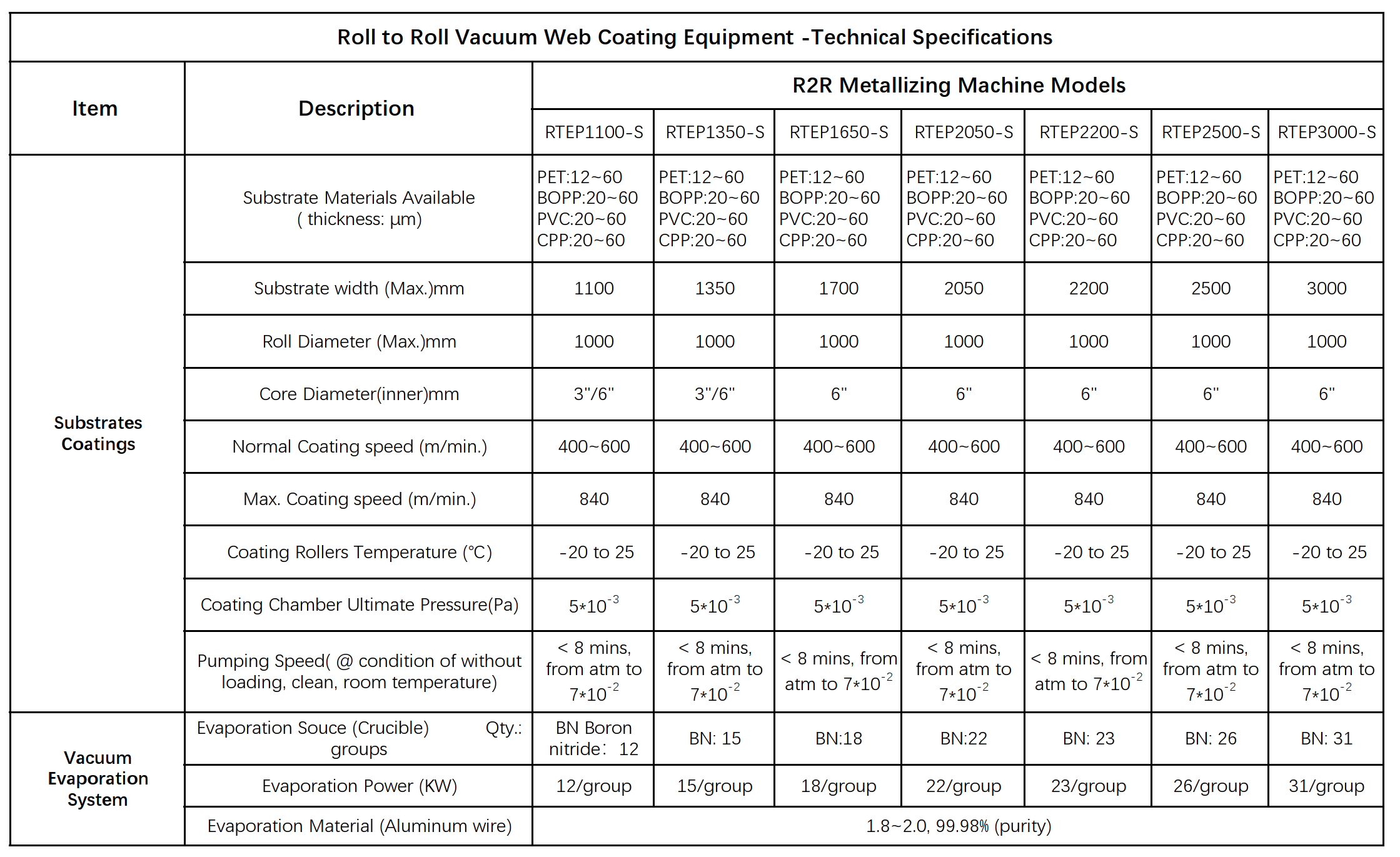
Please contact us for more specifications, Royal Technology is honored to provide you total coating solutions.
R2R (Roll-to-Roll) web aluminum vacuum metallizers are machines used in the manufacturing industry for depositing a thin layer of aluminum onto flexible substrates in a continuous roll-to-roll process. This process is commonly employed in various industries, such as packaging, electronics, automotive, and decorative applications.
General Information
Royal Technology serves our customers in films and paper package coating industries.
This series of high vacuum web coating systems are designed for the coating of rolled paper, BOPP, CPP, PET, PE films with aluminum thin layer in a vacuum ambient.
They are especially designed for the coating of one side of substrates to be used as packaging material and similar applications.
How to design the R2R web vacuum metallizing system?
Designing a web vacuum metallizer, specifically an R2R (roll-to-roll) system, involves several considerations. Here's a general overview of the design process:
1. Determine the Specifications: Define the specific requirements for your metallizer, such as the web width, deposition materials, target deposition rate, coating uniformity, and desired web speed. These specifications will guide the overall design.
2. Vacuum Chamber: Create a vacuum chamber that can accommodate the desired web width and length. Consider the material for the chamber, such as stainless steel, with appropriate seals to maintain a high vacuum level. Include access ports for loading and unloading the web.
3. Web Handling System: Design a robust web handling system capable of accommodating the desired web speed and tension control. This system includes unwinding and rewinding modules, web guidance, tension control mechanisms, and web tracking systems to ensure accurate positioning during the coating process.
4. Web Cleaning and Pre-treatment: Incorporate a web cleaning system to remove any contaminants before deposition. This may involve techniques like corona treatment, plasma cleaning, or UV/ozone treatment to enhance adhesion.
5. Evaporation Sources: Determine the type and number of evaporation sources based on the deposition materials. Common sources include resistance evaporation boats, electron beam evaporators, or magnetron sputtering sources. Consider factors such as material compatibility, deposition rate, and evaporation uniformity.
6. Substrate Heating: If necessary, include a substrate heating system to control the temperature of the web during deposition. This is important for certain applications or materials that require specific temperature conditions.
7. Vacuum System: Design a vacuum system capable of achieving and maintaining the required vacuum level. This typically includes mechanical pumps for roughing and high-vacuum pumps like turbomolecular pumps, high vacuum oil diffusion pump, or cryogenic pumps for achieving the desired vacuum environment.
8. Power Supplies and Control Systems: Select and integrate power supplies for heating the evaporation sources and controlling their deposition rates. Additionally, implement a comprehensive control system to monitor and manage various parameters such as web speed, web tension, deposition rate, and vacuum level.
9. Safety Measures: Incorporate safety features such as interlocks, emergency stop buttons, and appropriate shielding to ensure operator safety during operation.
10. Monitoring and Quality Control: Include monitoring and quality control systems to measure and verify coating thickness, uniformity, and other relevant parameters. This may involve optical sensors, quartz crystal microbalances, or other suitable measurement techniques.
11. System Integration and Testing: Assemble the components, integrate the subsystems, and thoroughly test the metallizer to ensure it meets the desired specifications. Conduct trials and optimize the process parameters for achieving the desired coating performance.
It's important to note that designing a web vacuum metallizer is a complex task that often requires specialized knowledge and expertise. Consider consulting with experts in the field or working with a company experienced in manufacturing such systems to ensure a successful design and implementation.
R2R (Roll-to-Roll) web vacuum metallizing equipment is utilized in various applications across industries. Some of the common applications include:
1. Packaging: R2R web vacuum metallizing is extensively used in the packaging industry to enhance the visual appeal and functionality of packaging materials. Metallized films are employed for flexible packaging, such as snack bags, candy wrappers, and pouches, to provide a glossy, metallic appearance, improve barrier properties, and offer moisture resistance.
2. Decorative Applications: R2R web vacuum metallizing is employed for decorative purposes in industries like automotive, electronics, appliances, and consumer goods. It allows manufacturers to create metallic finishes on plastic components, trims, nameplates, and other decorative elements, providing an attractive appearance and a premium feel.
3. Reflective Coatings: Vacuum metallizing is used to deposit reflective coatings on various substrates for applications such as mirrors, reflective films, and reflector surfaces for lighting fixtures. The reflective properties of the metallized coatings make them ideal for enhancing light reflection and increasing efficiency in optical systems.
4. Electronics: R2R web vacuum metallizing finds application in the electronics industry for producing conductive coatings, EMI/RFI shielding, and reflective coatings for displays. Metallized films are utilized in touchscreens, flexible circuits, electronic components, and printed circuit boards (PCBs) to provide electrical conductivity and electromagnetic shielding.
5. Solar Energy: Vacuum metallizing is employed in the production of solar energy systems. Metallized coatings can be applied to solar reflectors and mirrors used in concentrated solar power (CSP) plants to improve sunlight reflectivity and enhance energy capture.
6. Anti-counterfeiting: Metallized coatings can be used as security features in banknotes, labels, and packaging to prevent counterfeiting. The reflective and visually distinctive characteristics of metallized coatings make them difficult to replicate accurately.
These are just a few examples of the applications of R2R web vacuum metallizing equipment. The versatility of the process allows for a wide range of possibilities in terms of functional and decorative coatings on flexible substrates.
Technical advantages
Features
The web coating system adopts advanced round chamber structure, the vacuum chambers contain winding( top chamber)
and evaporation chambers (under); winding/unwinding devices are located in the same side of vacuum chamber, which guarantee |
||||||||
High efficiency vacuum pumping system for a short vacuum evacuation cycle, improve the productivity efficiently. | ||||||||
The web coating system equips with holding pump to ensure energy saving | ||||||||
The deposition chamber, winding chamber are equipped with powerful cold trap pumping system, which can effectively drain
the vacuum chamber and substrates moisture (temperature-120℃, the total area of the cold trap coil 2 ㎡, which improves the |
||||||||
The winding system adopts four-motors constant tension control system | ||||||||
To ensure the web film’s winding speed adjust is steady, the web coating system equipped with Siemens servo motors and servo speed regulator | ||||||||
The high performance SPREADER ROLLERS can adjust the angle according to changes during the coating process to ensure the substrate rolls flatness. |
||||||||
The coating roller, from room temperature till -15℃, its cooling and heating system can prevent film’s thermal damage during deposition process. Also can open the spreader roller in vacuum chamber to absorb moisture on the roll surface. |
||||||||
The swing frame structure can adjust the winding process automatically according to winding roll’s diameter, to ensure an equal distance winding. | ||||||||
Evaporation system designed with staggered and end face clamping structure for a high deposition rate, fast deposition boats changing and good contact which ensure the high quality of uniformity, shorten the auxiliary equipment’s working time and improve working efficiency. |
||||||||
Independent aluminum wire feeding system, according to different coating process requested, both individually wire feeding for each group and overall adjustment are available. |
||||||||
The web coating system’s fault alarm device provides trouble shooting tips, convenient for operator and maintenance engineer to find out and fix the troubles, back to normal production quickly. |
Free span and drum supported coating system
R2R web vacuum metallizers can be designed with different configurations, including FREEN SPAN and drum-supported coating systems. Here's how these two configurations differ:
1. FREEN SPAN Configuration: In a FREEN SPAN configuration, the web (substrate) is held taut and travels freely between two or more vacuum chambers. The web is typically supported by rollers or belts, and the tension is carefully controlled to ensure precise movement and uniform coating deposition. The chambers are designed to accommodate the web width, and the vacuum process occurs while the web is in motion.
Advantages of FREEN SPAN configuration:
· Continuous Coating: The continuous movement of the web allows for continuous coating deposition without interruptions, resulting in high production throughput.
· Uniform Coating Thickness: The controlled tension and smooth movement of the web help achieve uniform coating thickness across the entire web surface.
· Flexibility: FREEN SPAN configurations can handle a wide range of web widths and materials, providing flexibility in production.
2. Drum-Supported Coating Configuration: In a drum-supported coating configuration, the web is wrapped around a rotating drum or cylinder, which serves as the primary support for the substrate during the vacuum metallization process. The drum is typically perforated to allow for the passage of vapor and facilitate the deposition of the metal layer onto the web.
Advantages of Drum-Supported coating configuration:
· Simplified Handling: The drum provides a convenient and robust support structure for the web during the coating process, simplifying handling and alignment.
· Reduced Web Tension: The drum-supported configuration allows for lower web tension compared to FREEN SPAN systems, which can be beneficial for delicate or sensitive substrates.
· Enhanced Coating Coverage: The drum's rotation facilitates uniform coating coverage on the entire web surface as it passes through the metallization process.
Both FREEN SPAN and drum-supported coating configurations have their advantages depending on the specific application requirements. The choice of configuration often depends on factors such as web width, substrate type, desired coating quality, and production volume. Manufacturers select the configuration that best suits their needs to achieve optimal coating results and production efficiency.